ACU-T: 1000 HyperMesh CFD UI Introduction
This tutorial introduces you to the workflow for setting up a Computational Fluid Dynamics (CFD) analysis using Altair HyperMesh CFD. HyperMesh CFD is a powerful tool which provides a single, streamlined platform for performing a CFD analysis, starting from importing CAD through post-processing results. In this tutorial, you will learn how to use HyperMesh CFD for setting up a CFD analysis while exploring different capabilities available within the software for importing a geometric model, validating the geometry, setting up simulation parameters and boundary conditions, and generating a mesh. You will then launch AcuSolve simulation directly from HyperMesh CFD and post-process the results using HyperMesh CFD Post.
Prerequisites
To run this simulation, you will need access to a licensed version of HyperMesh CFD and AcuSolve.
Analyze the Problem
An important step in any CFD simulation is to examine the engineering problem at hand and determine the important parameters that need to be provided to AcuSolve. Parameters can be based on geometrical elements, such as inlets, outlets, or walls, and on flow conditions, such as fluid properties, velocity, or whether the flow should be modeled as turbulent or as laminar.
Figure 1. Schematic of the Problem
Introduction to HyperMesh CFD
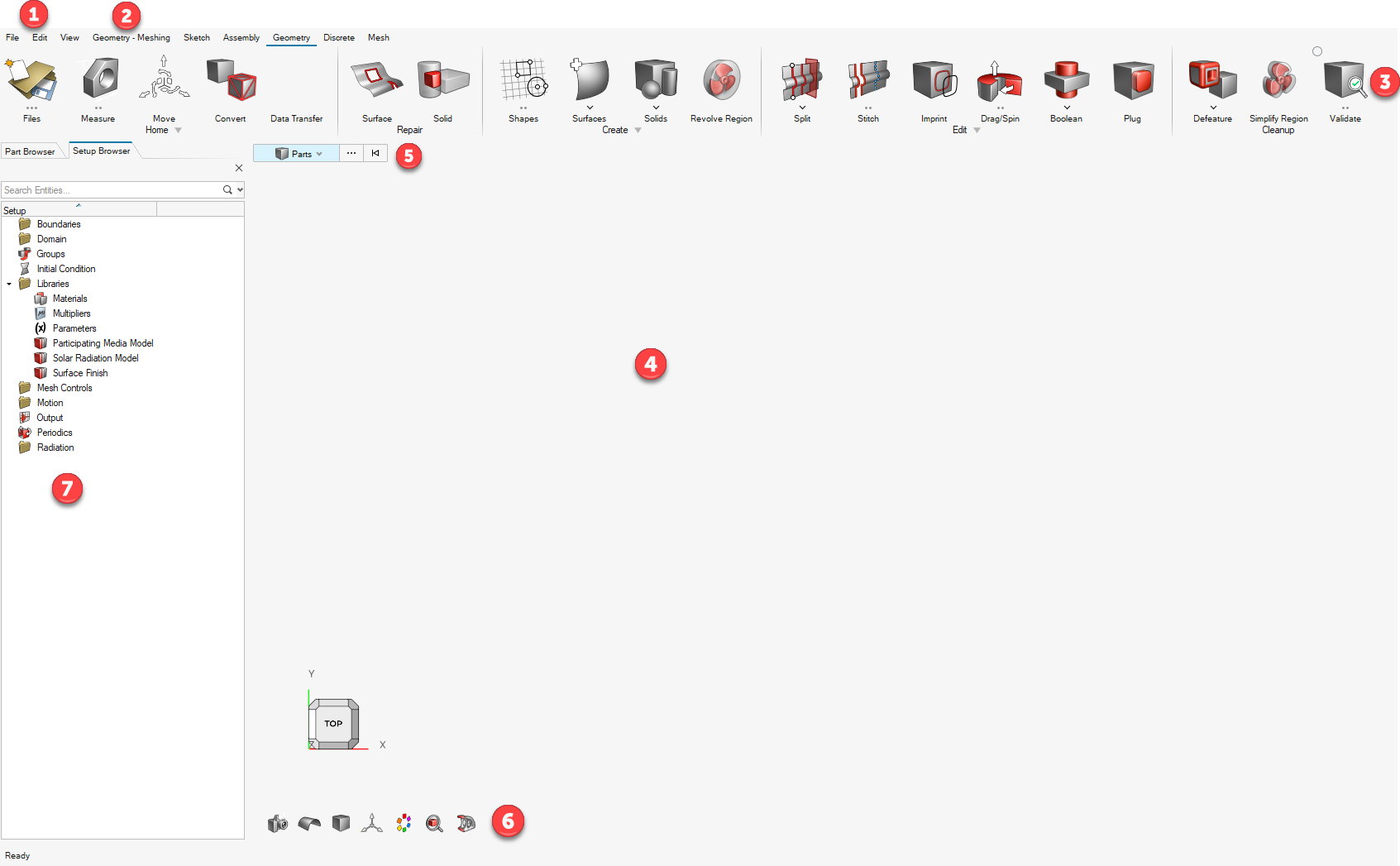
Figure 2.
The HyperMesh CFD graphical user interface can be divided into seven general categories as shown in the figure above.
- The menu bar contains the drop-down menus for File input-output, Edit, and View operations.
- The modeling environment switcher is used to populate relevant ribbons and tools based on modeling tasks.
- Ribbons contain various functionalities and tools available in HM-CFD. Navigate
between various ribbons by clicking the ribbon tabs to the right of the modeling
environment switcher. After selecting a ribbon, the corresponding tool icons are
displayed on the screen. The functionalities of various ribbons and corresponding
tools are briefly explained in this section.
- Sketch ribbon
- The Sketch ribbon provides multiple ways to define sketching plane
by selecting planes aligned with global coordinate systems. You can
also get references of existing geometry by cutting geometry or
projecting geometry to a plane. It provides capabilities to create
sketches using multiple interactive tools. A dimensioning capability
enables you to parametrize dimensions of sketches. One of big use
case for CFD is to get cutting lines of rotating geometry and create
a non–cylindrical axisymmetric MRF region around them.
Figure 3. - Geometry ribbon
-
The Geometry ribbon consists of tools for repairing, creating, editing, and validating the geometry.
When a geometry file is imported, the Repair tools can be used to detect any defects present in the CAD model like intersections, free edges, duplicates, sliver surfaces, and so on and fix those errors.
The tools available under the Create sub-section can be used to create geometric entities like points, lines, surfaces, and solids.
The tools required for performing operations like plugging cavities, stitching surfaces, and so on are available under the Edit sub-section.
The Defeature tool can be used to resolve defects or model a new geometry, while the Validate tool can be used to detect any defects present in the CAD model. This process is usually known as CAD cleanup.
Figure 4. - Discrete ribbon
-
The Discrete ribbon consists of tools used for working with FE geometry. You can cap openings, connect geometry, define local or proximity-based wrap controls, enclose the model, remesh the enclosed results, and fix the mesh quality.
- Assembly ribbon
- The Assembly ribbon is useful for finding, managing, and organizing the parts in your model.
- Flow ribbon
-
The Flow ribbon contains tools for setting up simulation parameters, solver settings, and reference properties such as material properties, heat sources, porous media, and so on. The Setup sub-section is where you set up the physics equations and solver settings as well as create material models, multiplier functions, and parameters.
Figure 7.The Domain sub-section contains tools for assigning reference properties such as materials, heat and momentum sources, and reference frames to volumes.
Figure 8.Surface boundary conditions such as inlets, outlets, and far fields, can be assigned using the tools under the Boundaries sub-section. By default, all the surfaces are assigned a boundary condition of type ‘auto_wall’ and are placed under Default wall. Refer to the AcuSolve Surface Processing manual for more information about auto_wall. As you assign boundary conditions to the surfaces, they are moved into the respective group.
Figure 9. - Radiation ribbon
-
The Radiation ribbon is where you define radiation physics, create thermal, solar, and participating media models, and apply radiation parameters.
Figure 10. - Motion ribbon
-
Mesh boundary conditions and mesh-motion-related parameters can be defined using the tools available in the Motion ribbon. Parameters such as mesh motion type and mesh displacement constraints can be defined here. In addition to the mesh boundary conditions, code coupling with external codes such as OptiStruct and MotionSolve can be defined here
Figure 11. - AcuTrace ribbon
- The AcuTrace ribbon computes particle
traces as a series of segments solving particle motion. It computes
traces for unsteady as well as steady flow fields, for flows with
mesh motion as well as without, and for flows computed on meshes
with interface surfaces. To solve a problem with AcuTrace, you must first run AcuSolve. You can set up for finite mass and
massless particles.
Figure 12. - Mesh ribbon
-
Meshing parameters such as surface mesh controls, boundary layer parameters, volume mesh parameters, and zone meshing parameters can be defined here. This ribbon also has tools for local remeshing. Once all the mesh controls are defined, you can generate the mesh using the Volume tool.
Figure 13. - Aerodynamics and Aeroacoustics Setup
- The setup ribbon is used carry out external aerodynamics and fan
noise simulations with the ultraFluidX
solver.
Figure 14. - Solution ribbon
-
The Solution ribbon is used to set up monitors for any individual point, surface, or volume set output. The Field tool is used to set the nodal output frequency for the entire model. The Initialize tools are used to set the nodal initial conditions for variables like pressure, velocity, and variables specific to each turbulence model.
Figure 15.Once the complete set up is done, the Run tool is used to launch AcuSolve. Once the AcuSolve run parameters are set, the simulation can be started, and you can monitor the status of the run using the run manager.
- Post ribbon
- The Post ribbon is where you can post-process the results. The
Visualize tools under the Post ribbon can be used to create things
like plots, streamlines, iso surfaces, and section cuts. The
Measures tools can be used to probe variables at desired
locations.
Figure 16. - Morphing Ribbon
- The Morphing ribbon is used to morph mesh or FE geometry. You can define constraints to fix some nodes or define relative movement.
- The modeling window is where the model is displayed. The
model display can be manipulated using the view controls shown in the table below.
Clicking on the model will highlight the entity being selected and right-clicking on
an entity will give you additional options for the operations that can be done based
on the context. Some of the functions available using right-click are Show, Hide,
Isolate, Select, Advanced select, Create groups, and so on.
Button Operation Middle mouse scroll Zoom in and out Right-click hold and drag Pan the model Middle mouse click hold and drag Rotate the model Left-click Select entity Ctrl + Left-click Select multiple entities Left-click hold and drag Window select Shift + Left-click Deselect entities - The entity selector enables you to control what entities can
be selected using the left-mouse button. The selector can be set to any of the
entities shown in the figure below. When you open any tool, the selector is
automatically set to the entity (entities) which are appropriate for that
command.
Figure 18. - The visualization of the model can be controlled using the tools available in View
Controls toolbar. The display of mesh, model coloring, section cuts, standard views,
and so on can be controlled using these tools.
Figure 19. - The browsers show the entities and setup parameters in the model and list them in a tree structure. They can be turned on or off from the View menu. Some common functions that can be performed in all browsers are show, hide, and isolate.
Start HyperMesh CFD and Create the HyperMesh Model Database
Import and Validate the Geometry
Import the Geometry
Validate the Geometry
Set Up the Problem
Set Up the Simulation Parameters and Solver Settings
Assign Material Properties
Assign the Flow Boundary Conditions
The current model has one inlet, three outlets, and walls for the rest of the surfaces. When a geometry model is imported into HyperMesh CFD, all the surfaces are placed in the Default Wall (i.e. Type = auto_wall). As you start assigning the surface boundary conditions, those surfaces are moved into a new boundary condition group. All the surface boundary condition tools are placed under the Boundaries sub-section of the Flow ribbon.
Define Mesh Controls
Now that you have assigned the material properties and boundary conditions, you will define the meshing parameters for the model and then generate the mesh.
Define the Surface Mesh Controls
Define the Boundary Layer Mesh Parameters
Generate the Mesh
Run AcuSolve
Post-Process the Results with HyperMesh CFD Post
This part of the tutorial shows you how to work with a steady state solution using HyperMesh CFD Post.
Load the Results
Create Pressure Contours on Boundary Surfaces
Plot Velocity and Pressure Contours on a Section Cut
Summary
In this tutorial, you worked through a basic workflow to carry out a CFD simulation and post-process the results using HyperMesh CFD. You started by importing the geometry and meshing the model in HyperMesh CFD. You also set up the model and launched AcuSolve directly from within HyperMesh CFD. Upon completion of the solution by AcuSolve, you post-processed the results in the Post ribbon. You learned how to create contours on the boundary surfaces and section cuts.