Single-Phase Nucleate Boiling in a Rectangular Channel
In this application, AcuSolve is used to simulate the wall heat flux due to nucleate boiling at a heated wall inside a rectangular channel with water flow. Results are compared with experimental heat flux measurements as reported by Steiner, et al. (2005). The close agreement of AcuSolve results with experimental results validates the ability of AcuSolve to model single phase nucleate boiling problems.
Problem Description
The problem consists of a channel with a heated wall at the bottom. The temperature of the wall is selected to onset the nucleate boiling at the heated wall. The dimensions of the inlet are 0.03 x 0.04 m; the inlet velocity (v) is 0.39 m/s and the temperature (T) of the fluid entering the inlets is varied from 373.15 K (100 C) to 406.15 (133 C) ), while the atmospheric pressure is specified to be 2 bar. The pre-heated water enters the inlets and heat is transferred into the fluid from the heated walls. The heat causes sub-cooled boiling to occur in the region close to the wall and leads to the formation of bubbles at nucleation sites. The surface tension and vapor phase models are specified to emulate the physical process of water changing state to water vapor.
The heat transfer in this regime is dominated by two effects, the macro convection due to the motion of the bulk liquid and the latent heat transport associated with the evaporation of the liquid micro-layer between the bubble and the heated wall. Each of these effects are modeled with AcuSolve and the prediction of their processes is demonstrated in the following results.

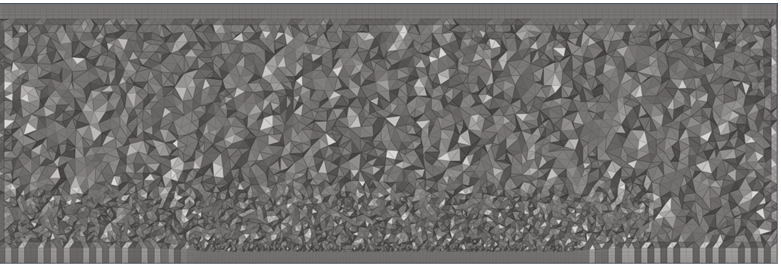
AcuSolve Results

Summary
The AcuSolve solution compares well with experimental results for single-phase nucleate boiling simulations. In this application, heat flux generated by the wall as the onset of boiling approaches are simulated with AcuSolve using the nucleate boiling feature and the RKE turbulence model. The experimental values of heat flux for the wall temperature range are presented with the corresponding AcuSolve results. A good agreement of simulation results with the experiment validates the ability to solve single-phase nucleate boiling using the nucleate boiling capabilities of AcuSolve.
Simulation Settings for Single-Phase Nucleate Boiling in a Rectangular Channel
HyperMesh CFD database file: <your working directory>\channel_single_phase_boiling\channel_single_phase_boiling.hm.
Global
- Problem Description
- Analysis type – Steady
- Turbulence equation – RKE
- Temperature equation – Advective Diffusive
- Nucleate Boiling Single Phase – On
- Auto Solution Strategy
- Convergence Tolerance – 0.001 sec
- Relaxation factor – 0.4
- Surface Tension Model (“Water-srfTns”)
- Type – Constant
- Surface Tension – 0.07
- Material Model
- Vapor
- Type – Constant
- Density – 1.128 kg/m3
- Viscosity – 1.29e-5 kg/m-sec
- Specific Heat – 2174.59 J/kg-K
- Latent Heat – 2256000
- Latent Heat Temperature – 393.45 K
- Conductivity – 0.02749 W/m-K
- Turbulent Prandtl number – 1.0
- Water
- Type – Constant
- Density – 965.36 kg/m3
- Viscosity – 0.000314 kg/m-sec
- Specific Heat – 4204.8 J/kg-K
- Conductivity – 0.675 W/m-K
- Turbulent Prandtl number – 0.91
- Vapor phase model – Vapor
- Surface Tension model – Water-srfTns
- Vapor
- Volumes
- Fluid
- Material– Water
- Fluid
- Surfaces
- Inflow
- Simple Boundary Condition – Inflow
- Inflow type – Average Velocity
- Average Velocity – 0.39 m/sec
- Temperature – 368.15 K
- Outflow
- Simple Boundary Condition – Outflow
- Back flow condition – On
- Temperature back flow type – Mass flux average
- Kinetic energy back flow type – Mass flux average
- Dissipation rate back flow type – Mass flux average
- Bottom
- Simple Boundary Condition – Wall
- Top
- Simple Boundary Condition – Wall
- Side_MinY
- Simple Boundary Condition – Wall
- Side_MaxY
- Simple Boundary Condition – Wall
- Heated Wall
- Simple Boundary Condition – Wall
- Temperature type – Value
- Temperature – [373.15, 378.15, 383.15, 388.15, 393.15, 398.15, 403.15, 406.15] K
- Inflow
References
Helfried Steiner, Alexander Kobor, Ludwig Gebhard, 2005, “A wall heat transfer model for subcooled boiling flow”, International Journal of Heat and Mass Transfer, Vol 48, pp. 4161- 4173.
Chen, J.C., 1966, “Correlation for Boiling Heat Transfer to Saturated Fluids in Convective Flow”, United States: N. p., 1962. Web. doi:10.2172/4636495.