Bearings#
Bearings are involved in almost all mechanisms, such as gearboxes, engines, robotic arms, and so on. In traditional multibody dynamics, bearings are often simplified by kinematic constraints, such as revolute joints or bushings. Kinematic constraints can lead to constraint redundancy that often results in some constraint being removed. While the kinematics of the mechanism are preserved, the load distribution between the bearings is wrongly represented. Similar issues can occur if bearings are represented by linear bushings, since the compliance of bearings is non-linear. Alternatively, bearings can be represented by a multibody subsystem, where raceways and rolling elements are represented by rigid or flexible bodies in contact with each other. However, those subsystems are computationally inefficient, especially if there are too many bearings within a mechanism. To overcome this impediment, MotionSolve contains bearing components designed particularly for system analysis. In other words, they were designed to accurately replicate the non-linear compliance of bearings but are simplified enough to accommodate the need for high-computational performance. The bearing components require only simple user inputs that can be found in many bearing catalogues. Use the results to study bearing loads and their life expectancy. The bearing components are developed on top of the MotionSolve API.
Each bearing consists of an inner and outer raceway that are defined as rigid bodies. Both raceways are connected to each other by a non-linear spring-damper system that represents the balls/rollers between the raceways. The spring-damper system is defined analytically using the Hertzian approach for point contact (balls) and the Palmgren formula for line contact (rollers). Its stiffness and damping properties are dependent on the relative position and velocity between the raceways. In the initial resting position, the local z-axis of the inner/outer race points along the shaft and the origin of the local frame is at the center of mass.
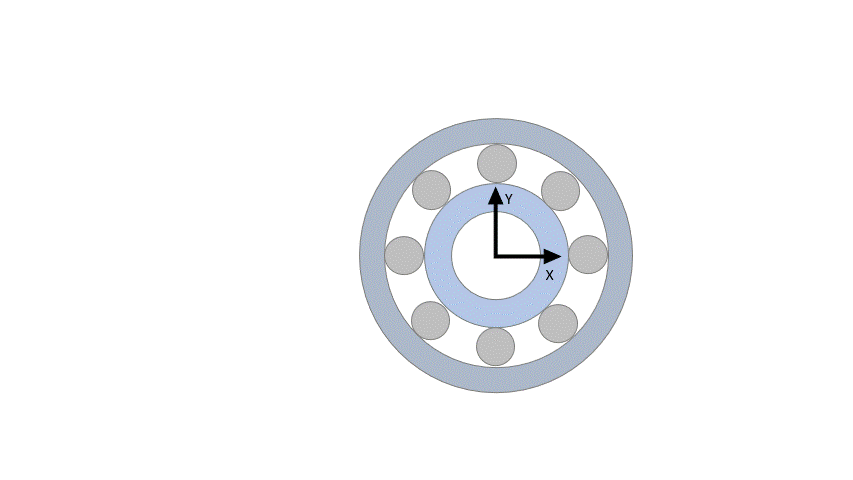
Figure 1. Description of the analytical bearing.#
The bearing’s cage and rolling elements are included as one rigid body. Its mass and inertia is approximated using the rolling element geometries. This rigid body helps estimate the overall weight of the bearing as well as visualize the rotation of the rollers.
Most of the machinery bearing’s input arguments can be extracted from catalogues and tables provided by bearing OEMs. Not all internal geometry parameters are provided in these tables directly, but instead need to be extracted from CAD geometry files that are provided by the OEMs.
Note
CAD files may not precisely capture the true geometry of a bearing. However, in most cases, the CAD files are a sufficient starting point for the bearing model.
The online OEM’s calculators can be used to extract many of the needed parameters, such as the type and the viscosity of bearing lubricants, or any calculation factor used for the friction torque calculation.
Bearing Types#
The msolve.machinery.bearings
library currently supports the following bearings:
Creates an analytical bearing that overtakes radial and axial loads in one direction. |
|
Creates an analytical bearing that overtakes the primary radial load. |
|
Creates an analytical bearing that overtakes the radial and axial loads in both directions. |
|
Creates an analytical bearing that overtakes the radial and axial loads in both directions. |
|
Creates an analytical bearing that overtakes the radial and axial loads in one direction. |