OS-E: 5005 Coupling Between Flux and OptiStruct
Demonstrate how the coupling between Flux 2D/3D and OptiStruct is performed for a vibro-acoustic analysis.

Figure 1. FE Model
Model Files
Model Description
The objective is to compute the magnetic force in Flux which will act as an input in OptiStruct for structural analysis or optimization.
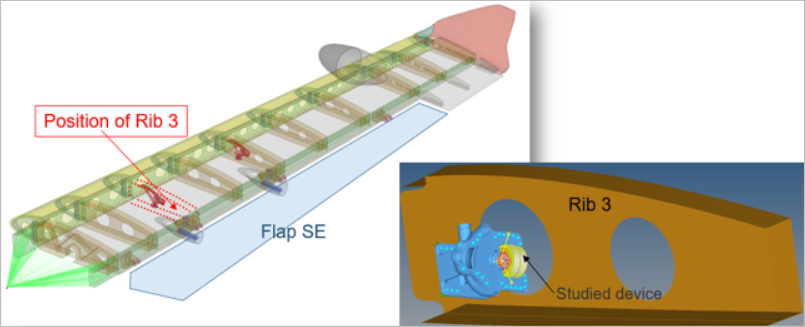
Figure 2.
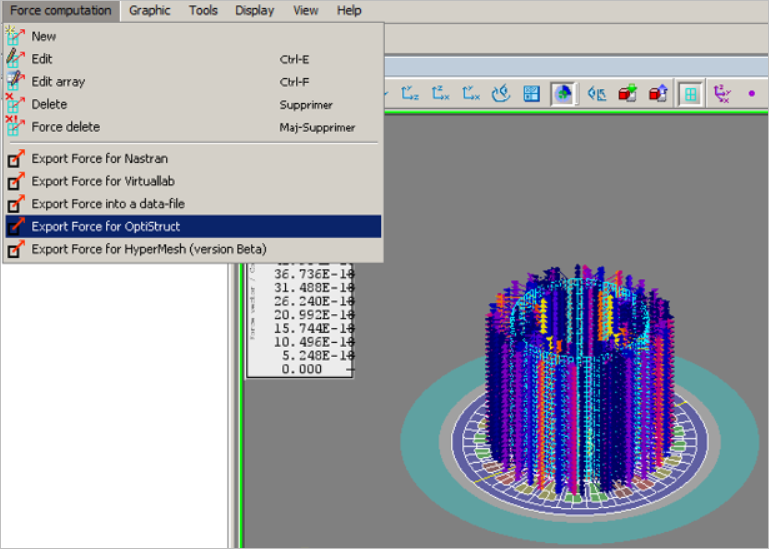
Figure 3. Forces extracted from and the Equivalent Radiated Power (ERP) output
- For additional details regarding the input from Flux, refer to the Flux documentation.
- The forces from Flux are provided in the
cartesian coordinate system. As the forces are calculated using Flux2D,
there is no axial (Z) component of forces. Thus, in the nodes where
forces are applied, the calculations are performed in a cartesian
coordinate system and not in a cylindrical coordinate system.
Further, as the stator in the OptiStruct model is not oriented along the global Z axis, a local rectangular system is used to apply the loads in the correct directions.
Results
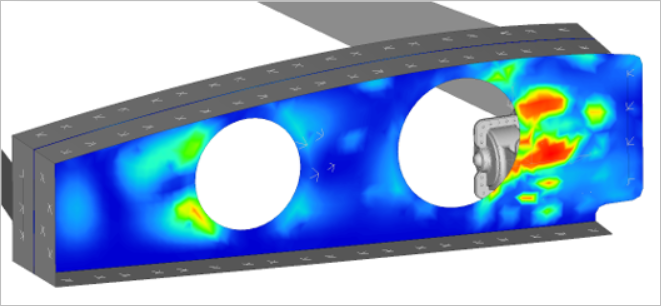
Figure 4. Equivalent Response Power (ERP) on the Wing Body
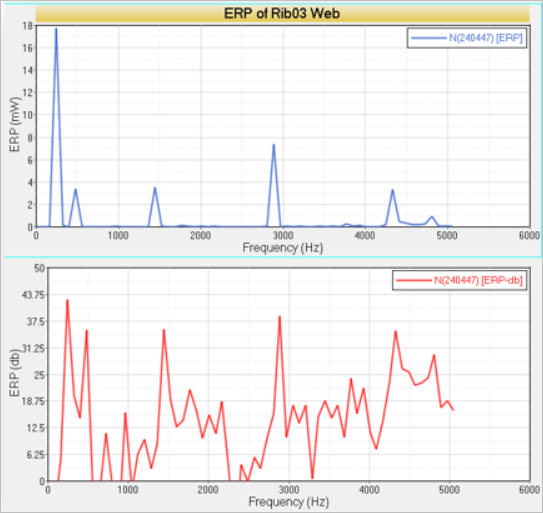
Figure 5. Variation of ERP (in mW and db) with Frequency