DVS 1612
Version: August 2014 Edition
List of Classification Parameters
- Evaluation Distance
- Reference distance to find the evaluation location from the weld element at which the stress values are extracted.
- Weld Width
- Width of the weld material from the web wall. This parameter is ignored if
specifying the evaluation distance is done manually.Note: Refer to - Find Evaluation Positions.
- Cutoff Value
- Used along with the material yield to determine the cutoff yield value to be
used.
Yield (cutoff) = Material yield / Cutoff value
- Notch Class - Transverse Location_X
- Notch class definition considered for the fatigue limit calculation for the
normal stress component in the transverse direction (perpendicular to the
axis of the weld) at ‘X’.Note: Where ‘X’ can be any evaluation location.
- Notch Class - Longitudinal Location_X:
- Notch class definition considered for the fatigue limit calculation for the normal stress component in the longitudinal direction (parallel to the axis of the weld) at ‘X’.
- Notch Class - Shear Location_X
- Notch class definition considered for the shear stress component at ‘X’.
- Material Grade - Location_X
- Grade of shell material used. Options – S355, S235. Also, interpolation for in between values is supported. Location specific.
- Material Yield - Location_X
- Material yield. Location specific.
- Groove Gap (b)
- Gap between the two plates at the location of weld. b in Figure 1.
- Groove Depth (h)
- Height of the groove from the top, calculated as t - c from Figure 1.
- Groove Angle (alpha - deg)
- Angle of the groove/plate walls at the location of weld. a in Figure 1. Note: Refer to Figure 1 for the groove parameters. These groove parameters have been derived from the En 15085 standard. Refer to Common Classification Parameters.
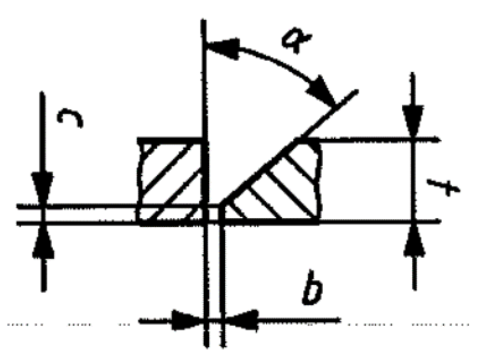
Figure 1.
Static Assessment
- Retrieve the six components of stress from the element at the evaluation location.
- Calculate the von Mises stress value using these stress components.
- Retrieve the material yield value from the Points context.
- Determine the static strength ratio: element von Mises stress / material yield value
Frequently Asked Questions
- What is the Cutoff Parameter?
- It is a safety factor to be used along the yield strength. This value is
used to determine the upper limit for the fatigue
strength.
Fatigue strength (cutoff) = Material yield / Cutoff value
- How does the exponent x interpolation work?
-
In case of DVS 1612, the value of exponent ‘x’ depends on the material grade and has different values based on the grades of S235 and S355. But, whenever the base/web material does not fall into either of these grades, then the tool uses an interpolation technique to find the intermediate ‘x’ exponent value.
Figure 2.- The tool retrieves the material grade/yield assigned for the particular location from the classification area.
- The tool also identifies the fatigue class/notch case for the particular location from the classification area.
- Based on this fatigue class, the tool retrieves both the values of exponent 'x' from the “regulation_ data” folder belonging to the grades S235 and S355.
- An initial check is carried out to determine if the material yield is higher than the highest grade (S355) or if it is lower than the lowest grade. If so, then the tool considers the exponent 'x' to belong to the highest/lowest grade respectively for calculation.
- If the material yield value is in between the two grades, then the tool calculates the intermediate value of exponent ‘x’ using a linear interpolation technique. The calculated value of exponent ‘x’ is then used for utilization calculation.
Figure 3.