Thermal Effects (Combined) Analysis
Evaluate squeak and rattle issues when exposed to thermal loading.
A typical challenge faced in the automotive industry is how does the vehicle interior perform under driving conditions while the vehicle has been parked in the sun for many hours?
To answer this question, vibration loads responses (Dynamics) need to be superposed to the temperature effect on parts (Thermal Expansion – Static), gaps are reduced for example. In this workflow, the user will evaluate the squeak and rattle issues in a dynamic condition where the vehicle, in this case, a parked under sunlight with a spike in internal temperature (Static loadcase). Later the car is driven, which is exposed to Dynamic Loading. Below is the illustration of the Driving Vehicle exposed to the Thermal Effects (Combined Loading) workflow.- Prepare the FE model for analyzing squeak and rattle issues.
- Apply a static load of amplitude -5.55 to the certain node(s) on Lower Control Panel component. This simulates a touch point scenario.
- Run analysis and post-process the results.
For this tutorial, you will use the solver deck exported from the Detailed Risk and Root Cause Analysis usecase. Once you import the Dynamic Loadcase solver deck, you can proceed with Thermal (Static) Loadcase setup.
Define Thermal Loadcase
In this step, you will create a thermal loadcase.
Define Constraint
In this step, you will define model constraints.
Import Model and Results File
In this step, you will use SnRD Post to post process the results.
Post Processing
In this step, you will perform a Full Analysis to understand the squeak and rattle risks in the model.
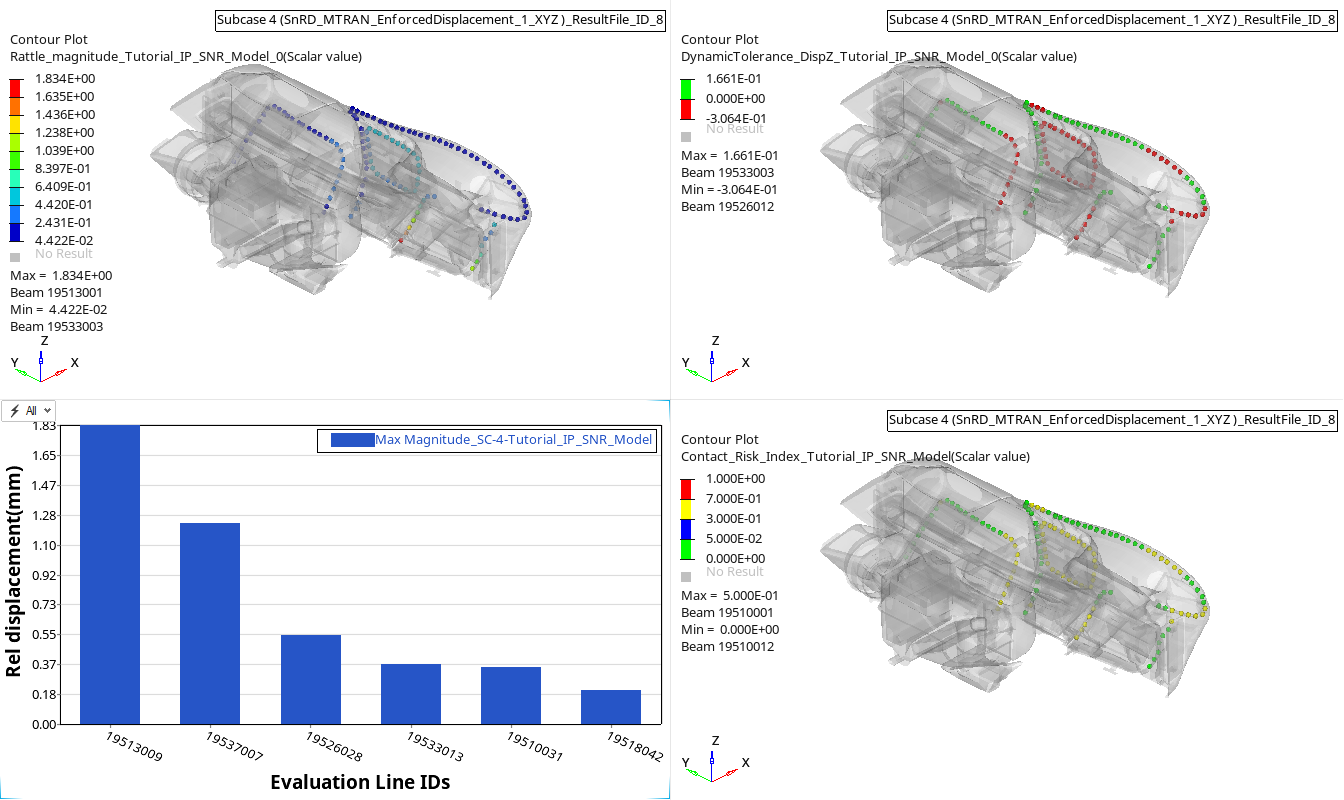
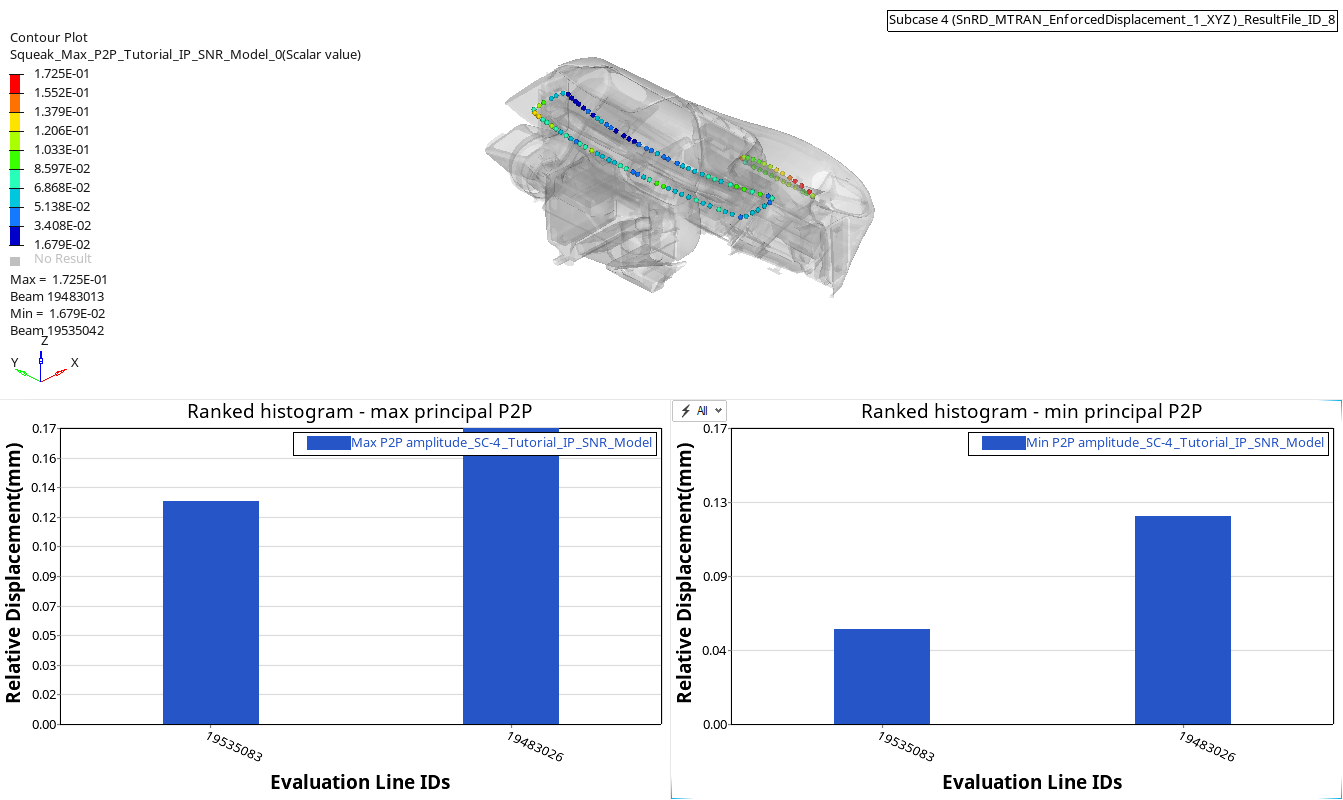
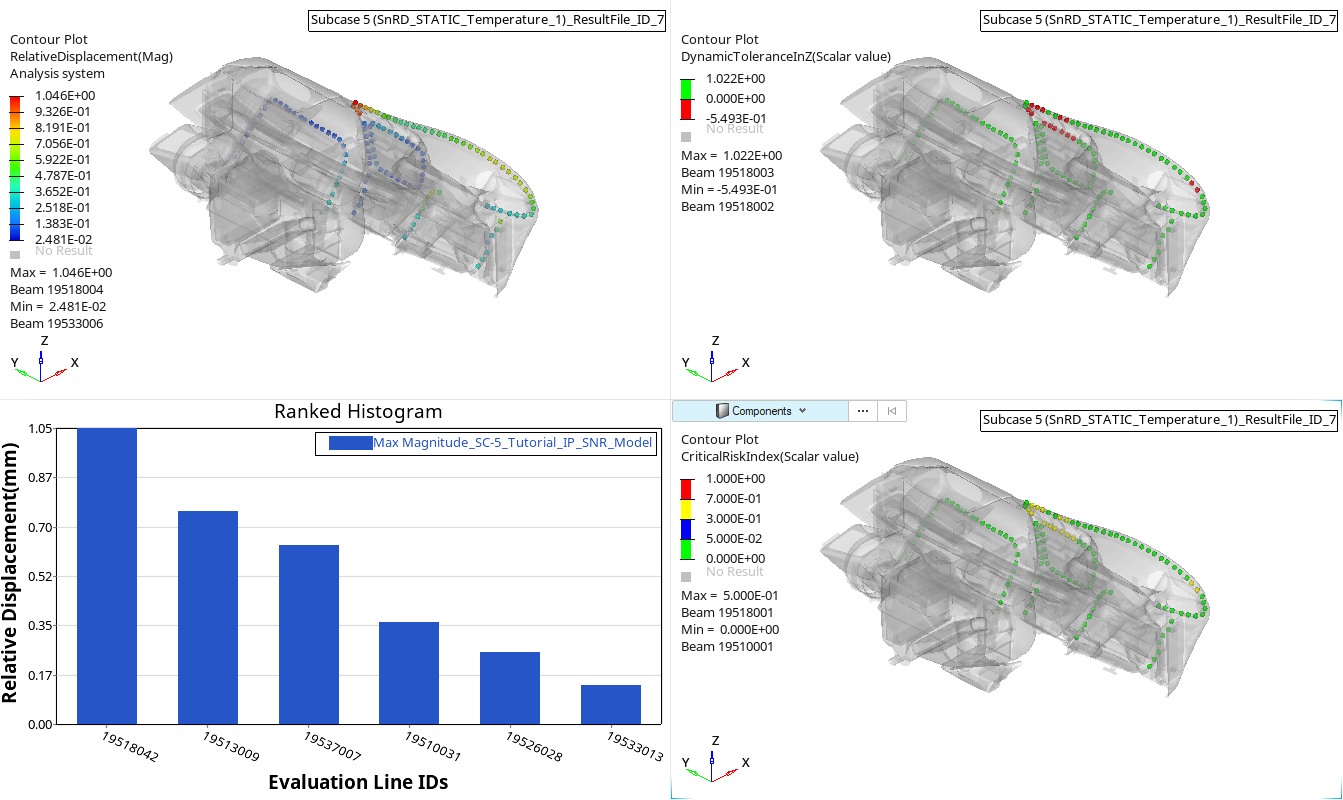
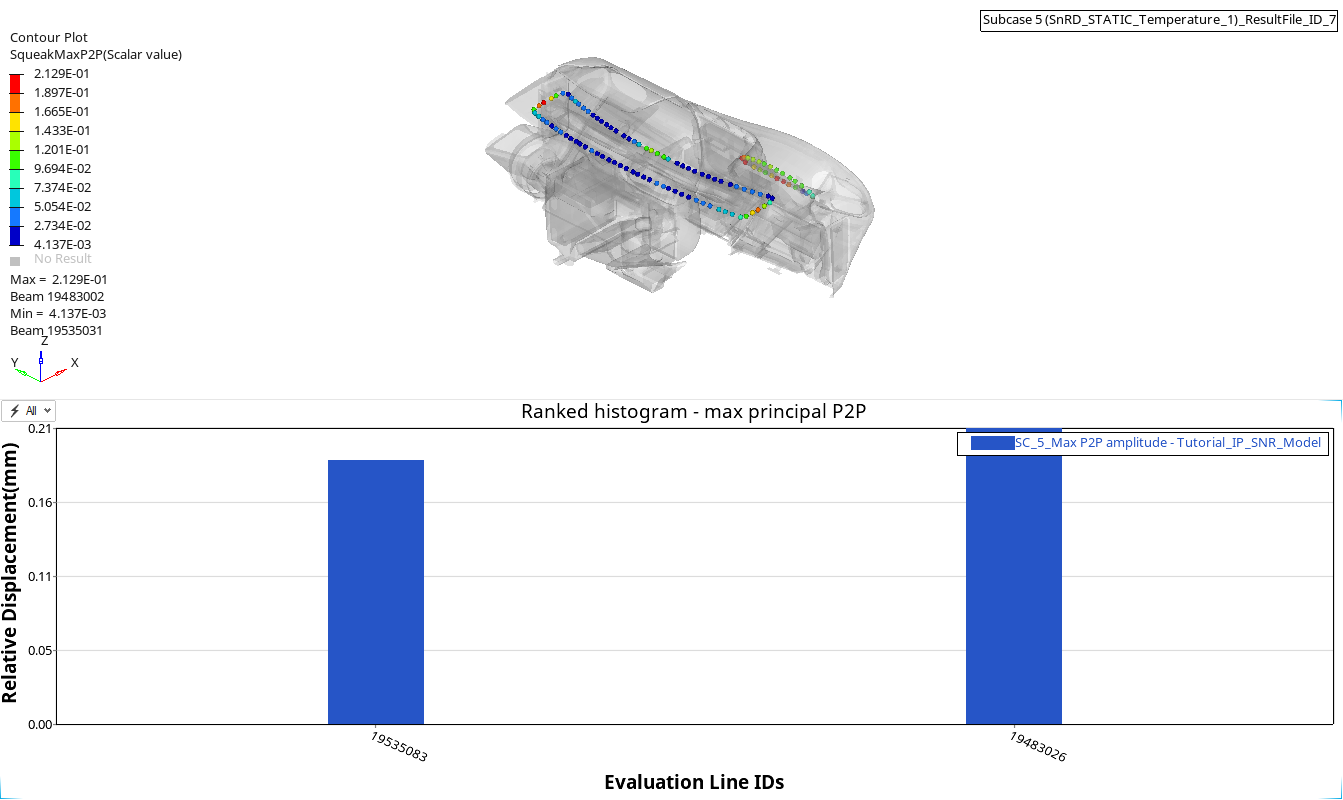
Combined Loading
In this step, you will perform a Combined Loading study to understand the thermal effects on the squeak and rattle issues under Dynamic Loading condition.