acm (detached-(T1+T2)/2)
Creates a hexa element with RBE3 (Nastran/OptiStruct) or DCOUP3D (Abaqus) elements projecting and connecting to the surrounding shell elements. This realization uses the shell thickness to calculate the hexa offset from the shell elements. In the case where the model is a 3T connection, the acm (detached-(T1+T2)/2) realization will not join the hexa elements.
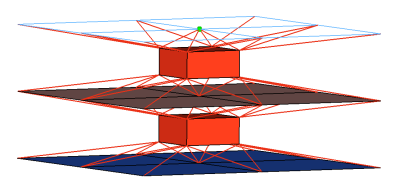
Figure 1.
ACM Realization Options
Option | Action |
---|---|
thickness | Select a thickness
option used for dimensioning and positioning hexas.
|
num hexas | Create a hexa cluster
with 1, 4, 8, 12, 16 or 32 hexas, which are arranged in a
predefined pattern.![]() Figure 4. Note: Available for all ACM realization
types.
|
coats | Define the number of hexa elements required along the thickness. Multiple solid coats are supported. |
orthogonal faces | Force the creation of
perfectly orthogonally-shaped hexas.![]() Figure 5. . The two leftmost realizations were performed with the orthogonal faces option enabled. Note: Available for any kind of ACM weld, if num hexas is
set to 1.
|